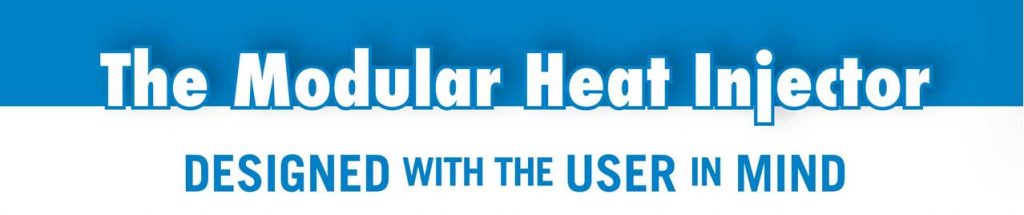
SAFE
The Heat Injector plugs into any standard home outlet. The electrical controls are UL Listed. The Flame Management System controls the redundant gas valves starts the burner and continuously monitors the flame. The Temperature Control System continuously monitors the discharge temperature and automatically modulates the gas to achieve the chosen discharge temperature.
SIMPLE
A switch enables the airflow, another switch enables the heat, and then it operates automatically. The discharge temperature is continuously monitored and automatically controlled to achieve the operator’s chosen discharge temperature.
EFFECTIVE
The Heat Injector uses a unique method to thoroughly heat the structure and its contents. When the temperature is above the lethal temperature for bed bugs, the pressurization process is engaged to force heated air through electrical sockets and any openings in the structure.
ENERGY EFFICIENT
The Heat Injector allows the main airflow to be recirculated and puts 100% of the heat into the space with only a small volume of outside air used for combustion. Other commercial bed bug heaters powered by propane, heat all outside air and force it into the heat treatment with ducts exposed to the outside environment and this method requires openings in the structure to exhaust heated air. Please see the energy comparison graphs…the method used to perform a heat treatment makes a big difference in the effective use of energy.
POWERFUL
The Heat Injector System puts more heat into a heat treatment than the largest electrical system or the tube style heaters that consume significantly more fuel. The discharge temperature is adjustable from the Control Panel, with a range up to 160°F.
DISCRETE
The Heat Injector System is positioned within an outside doorway or can be placed inside the heated environment with the use of the Air Shell. There is no generator, boiler, or external duct which would draw attention to your client. This feature makes this bed bug heat equipment a competitive advantage as compared to other bed bug heaters.
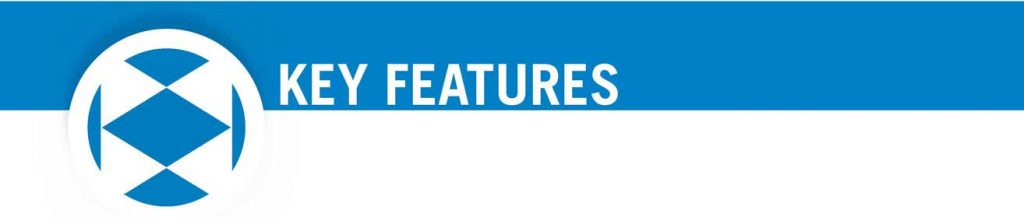
Most Energy Efficient Heat Treatment Process
The Heat Injector uses a patented heating process which allows it to produce the most energy efficient heat treatment for bed bugs!
Immediate Heat at Regulated Discharge Temperature
The heated discharge air is immediately brought up to operator chosen discharge temperatures; no warm-up time is required. When the full potential of the Portable Heat Injector is used to heat air, the burner is able to produce a temperature rise of 90°F with 4,000 CFM to produce 389,000 Btu of heat, equivalent to 114KW of electrical power. This patented concept allows the volume of air through the injection chamber to be varied without having an effect upon the clean-burning characteristics of the low emission direct gas-fired burner. The heating potential and variable airflow feature allow any intake air temperature to be discharged at the set-point temperature.
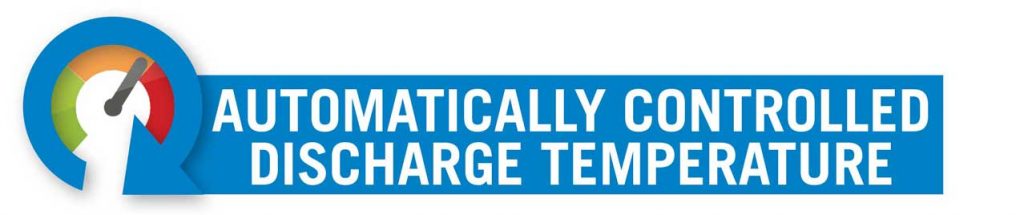
Controlled Discharge Temperatures
The Portable Heat Injector System has significant power and control over the amount of heat being injected to achieve a temperature rise from 3 to 90°F at full speed airflow. If more than a 90° temperature rise is required, the volume of air can be reduced to achieve the desired discharge temperature. The components used in the system are rated to handle a maximum temperature of 180° F. The Temperature Controller has Supervisory Limits for the temperature range to prevent settings above an acceptable level.
Discrete Heat Treatment
The ability to recirculate the heated air moves the heat through the structure and there are no external ducts or a noisy generator (the propane hose can be up to 400 ft.). The heat treatment is not obvious to the whole neighborhood because there are no external ducts and no noisy equipment. This feature makes it one of the most sought after professional bed bug heaters in the market.
Plugs into any house outlet
By utilizing cutting-edge technology, the Portable Heat Injector utilizes the typical 15-amp house outlet to power the 240v, 3phase Premium Efficiency 1.5 HP, Inverter Duty TEFC (totally enclosed, fan cooled) Motor. The main airflow blower, motor and the electrical controls were chosen to move the maximum volume of air from a standard outlet.

Pressurizes Treatment with Lethal Temps
When the space is thoroughly heated, it can be pressurized to force heat through openings like electrical outlet and any cracks in the structure where bed bugs might have found harborage…just open the Pressurization Gate and drop the Damper.
Purges Heat After Treatment
Positioning the Portable Heat Injector on the entrance of the structure allows the air intake to have access to fresh air. When the air intake is made to draw fresh air, it will create a high pressure within the structure at the point of discharge. The fresh air creates an airflow path within the structure to all open doors and windows within the structure. The purge is typically done without adding heat to allow the gas lines to be packed while cooling off the structure and its contents. The purge should continue until the temperature within the structure can be controlled by the existing HVAC System.
Motors and Controls are outside the Heat
The Portable Heat Injector System is to be positioned in a doorway to become a barrier to the heated environment or positioned inside the treatment area with an Air Shell during the heat treatment to keep the motors and controls outside the heated environment to ensure safety and long equipment life. These placements allow fresh air for the dedicated combustion blower to be drawn in around the control panel and across the combustion blower motor to ensure they are not subjected to the elevated levels of heat. The main blower motor is also located outside the heated environment with only the belts passing into the blower chamber. The belt slot is located in a low pressure area in the blower module to continually draw fresh air across the main blower motor.
Industrial Safety Systems on Board
The FM approved Flame Management System manages the flame and safety interlocks. The flame is continuously monitored with the fame rod amplifier with a 1-second response to a loss of flame signal. The direct spark ignition has a manual reset which is available from outside the control panel. A microprocessor-based temperature controller senses the discharge temperature to control the Gas Modulation System to achieve the desired discharge temperature (+/- 1°F) at any airflow available from the control panel adjustment. An independent high-temperature limit senses the discharge for added safety. The high-temperature limit switch is automatically reset after things cool down. A special key is required to access the control panel and burner controls to ensure that only authorized personnel can open the panels. This feature combined with others mentioned here makes it one of the safest bed bug heaters in the market.

Easy Operation and Maintenance
Many commercial bed bug heaters are complex to operate safely and require significant maintenance. Our patented bed bug heat equipment was designed with the user in mind and there is no specific maintenance that needs to be done on this equipment.
The airflow is controlled with a switch and the volume of air is controlled by adjusting a knob. The burner is engaged with a switch that is interlocked to the airflow. The burner can be started and operated at any airflow. The desired discharge temperature is controlled by toggling the set point displayed on the Temperature Controller mounted in the Control Panel Door.
The belt for the main airflow blower should be periodically monitored for tightness by viewing it through the air inlet. The soft start and stop of the VFD will cause the belt life to be extended. The redundant valves should be tested annually and test voltage for the flame rod amplifier should be recorded to see if the signal is becoming weaker which would indicate the soon replacement of the flame rod. The Igniter should also be visually inspected annually. A detailed Owner’s Manual is supplied with every purchase.
The Modular design make these bed bug heaters easy to repair if the need ever arises.
Applications
Our patented bed bug heat equipment is being successfully used by various types of pest control companies. Some had already been using other bed bug heat equipment prior to learning about the Heat Injector System while others transition directly to heat with the Heat Injector System when they saw how safe, simple and effective it was.
Our clients have taken on these challenges with the Heat Injector System:
- Call centers… a 35,000 sq. ft call center was treated in 48 hours with 2 Heat Injectors.
- Heat Treatment of shoe store and associated warehouse.
- Heat treatment in University housing and homeless shelters
- Heat treatment in motor homes and Semi-Trucks with sleeper cabs.
- Heat treatments in Water Park Suites
- Residential Homes of any size
- Commercial Properties and Nursing Homes
- Supplemental heat for water restoration process
- Hotels, motels and cabins